The international corrugated box standard, jointly established by the European Federation of Corrugated Board Manufacturers (FEFCO) and the Swiss Paperboard Association (ASSCO), sets the benchmark for corrugated box structural types. This standard, internationally recognized and approved by the International Corrugated Board Association, categorizes box structures into standard and non-standard types.
Standard Types:
In accordance with the international corrugated box standard, box structures are classified into basic and combination types.
1. Basic Types:
Basic types are typically denoted by a 4-digit code, where the first two digits indicate the box category, and the last two digits represent different styles within the same box type.
- 01 Type: Refers to single-face corrugated board rolls. For instance, 0100 type represents single-face corrugated board rolls used as cushioning material or can be converted into double-face corrugated board as in the 0110 type.
- 02 Slotted-Type Boxes:
The slotted-type boxes, exemplified by the tuck-in lid design, feature top and bottom lids. They also incorporate bottom inserts to prevent items from leaking out. These boxes are commonly used as outer packaging made from a single piece of corrugated board, with no separate top and bottom lids. The box blank is joined using methods like stapling, gluing, or tape sealing to form the box body, where the top and bottom lids conveniently serve as the box cover and base.
- 03 Nestable-Type Boxes:
This box structure typically comprises two or more pieces, with the "nestable" style being a common representation. A distinguishing feature is the separation of the lid from the box (sometimes including the bottom), offering good stacking strength and pressure resistance. The design involves calculating the base dimensions first and then determining the lid manufacturing dimensions based on the external dimensions of the base.
- 04 Foldable-Type Boxes:
These boxes are usually formed from a single sheet of cardboard through creasing and die-cutting, eliminating the need for stapling or gluing.
- 05 Slide-Type Boxes:
Also known as drawer-style boxes, they consist of internal boxes or frames along with an outer shell. Although more complex and time-consuming to manufacture, they are material-efficient and widely used for packaging mid to low-range products.
- 06 Bliss-Type Boxes:
Fixed boxes, commonly known as Bliss boxes, they represent three-dimensional boxes composed of two end panels and a main body panel joined by staples or other methods to form the box, with a solid bottom for convenient handling. They are suitable for packaging fragile items or larger goods but are time-consuming to produce.
- 07 Automatic-Type Boxes:
These boxes are formed from a single sheet with minimal adhesive, lying flat during transportation and storage (when empty). They automatically lock into shape upon opening, featuring a sturdy bottom suitable for large-scale manufacturing. Unlike type 03 tray-style automatic folding boxes where the body and lid are independently flat (when folded), they cannot be stacked flat after assembly.
- 08 Inner Liners:
This category includes various lining materials such as pads, partitions, and inserts among 45 different varieties.
Non-Standard Types:
1. Roll-Pack Type Box Structure:
The roll-pack type differs from the slotted box in corrugation orientation.
Roll-pack boxes are typically processed by high-speed automatic packaging machines for product coloring operations.
Advantages of Roll-Pack Boxes:
- Require less corrugated board compared to slotted boxes due to different opening directions.
- Provide tighter packaging than slotted boxes.
- Allow for variable-speed automated packaging.
Disadvantages of Roll-Pack Boxes:
- Lower compression strength compared to slotted boxes by about 20%.
- Increased corrugated board usage with height extension, impacting cost reduction.
- Suitable for mass production only.
2. Separable Box:
-01. Improved separable paper boxes:
a. Top surface connection method: Two slotted type boxes are sealed by a top panel, which can be separated by tearing the tape in the middle of the top panel.
b. Adhesive bonding method: Adhesive bonds the joints of two slotted type boxes together.
c. Insertion of connecting plates: Two slotted type boxes are connected on each side with an insert plate, which can be separated by tearing the tape in the middle of the insert plate.
d. Fixing method for the gap between connecting plates: Two or three paper boxes are placed side by side, and corrugated connecting plates are used to connect individual paper boxes on the top and bottom surfaces, forming a fixed combination box.
-02. New types of separable paper boxes (N, F, DP types):
Generally, H-shaped partition boards are inserted. The H-shaped partition board is combined with a wrapped paper box, and the box can be separated by tearing the tape on the wrapped paper box.
F-type wrapped paper boxes have the following advantages:
- Packaging units tend to be smaller and can be separated into two parts.
- Packaging strength is increased due to vertical corrugations on the side walls and an H-shaped partition board in the middle.
- Cost of packaging materials is reduced compared to other separable paper boxes, with approximately 20% less cardboard usage. The cost savings can reach 20-30% compared to slotted type boxes when considering partition boards.
DP-type wrapped paper boxes can be resealed after the box is disassembled.
-03. Triangular Column Box:
Triangular prism paper boxes have a unique structure where the corners of the box and the corner liners form triangular or right-angled prism structures, enhancing compressive strength by 20-50%. The key features of triangular prism corrugated paper boxes are:
a. Compared to standard corrugated boxes, the compressive strength is increased by 20-30% at room temperature (20°C, 65% RH) and by 40-60% in high humidity conditions (40°C, 90% RH).
b. The box remains free from bulging, especially noticeable in humid conditions.
c. The corner areas are sturdy, resulting in minimal damage to the contents during drop impact and vibration.
d. The box maintains stable deformation under load, reducing the risk of stack collapse.
e. Tray-type triangular prism corrugated paper boxes have good sales display characteristics.
-04. Large Boxes:
Large corrugated boxes can replace large wooden boxes, small containers, and bulk bags, and are mainly suitable for:
a. Large-sized goods
b. Combining medium-sized goods into large units
c. Arranging small items into large units
d. Powder and granular products
There are two types of large corrugated boxes:
-01. Hinged lid boxes:
Large hinged lid boxes, similar to type 02 boxes, are made of double corrugated, triple corrugated, or x-PLY (cross-stacked corrugated) super strong corrugated boards to enhance strength. Additional single, double, or triple corrugated cardboard liners can be added inside the box. To prevent deformation of the box bottom, a collapsible large box lid can be used. Conversely, if not subjected to heavy loads, packaging material can be saved by shortening the hinged lid and embedding a bottom board.
-02. Nesting boxes:
Nesting large boxes are similar to type 03 boxes, where rectangular or polygonal boxes are nested with top and bottom covers. They can replace metal boxes, deep nesting boxes, with heights reaching up to 2350mm. Due to the nature of the contents (powder or granular), rectangular box bodies may deform. To increase strength, nesting boxes often use polygons, primarily octagonal shapes.
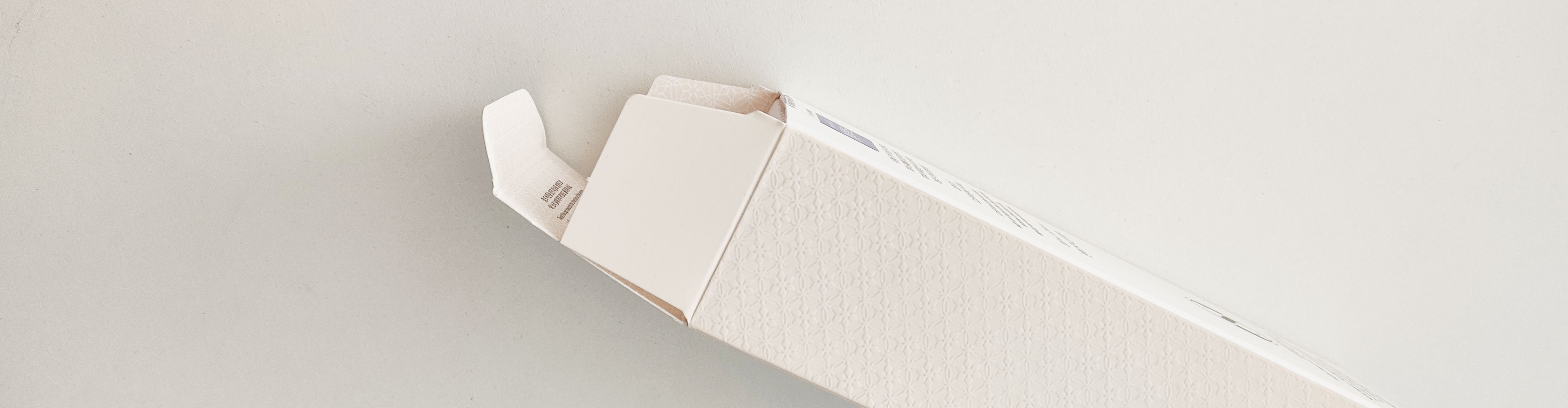
previous post
Folding cartons are versatile packaging solutions
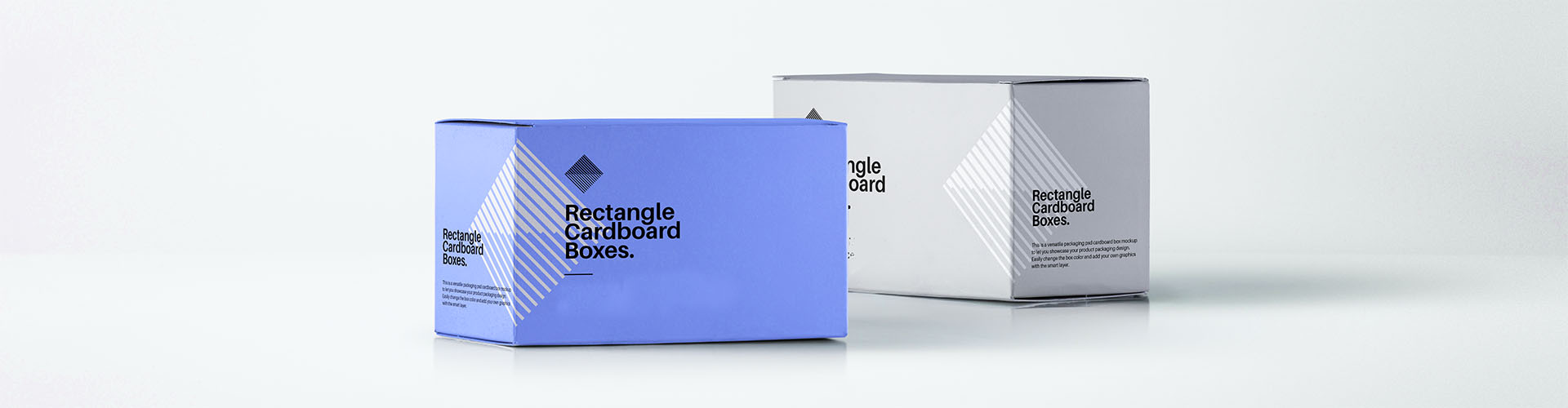
next post
The Trends of Folding Cartons in 2024 and Beyond
YOU MAY ALSO LIKE
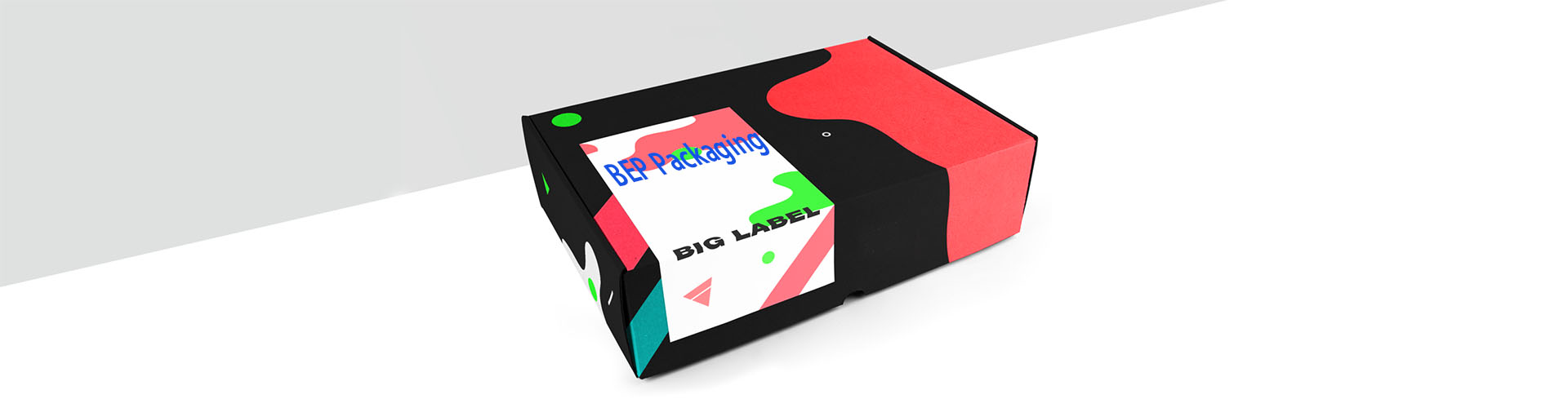
What is sustainable packaging
2023-05-05 02:03:21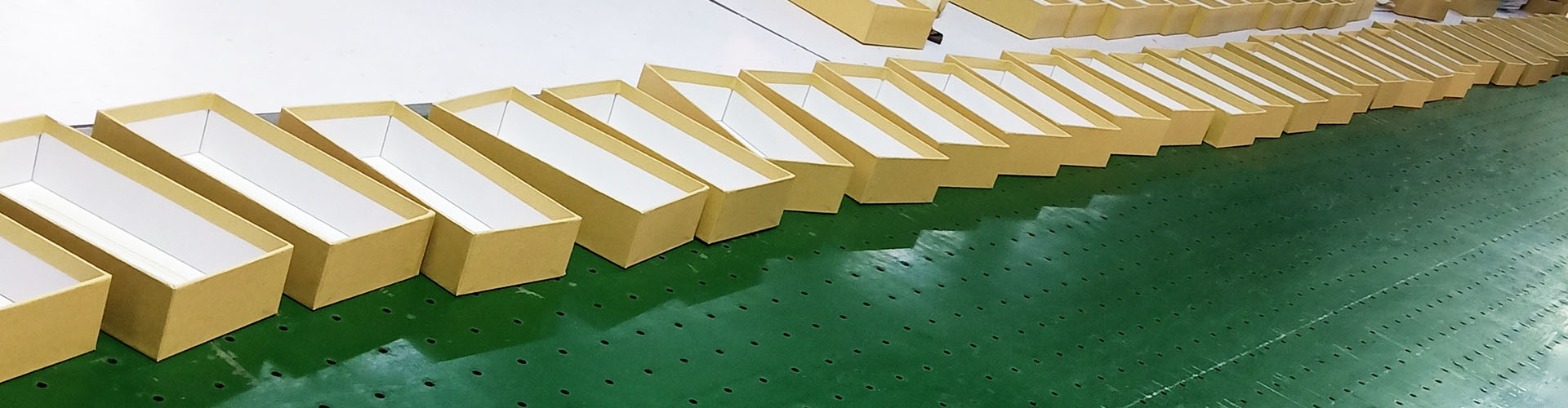
Integrated packaging solutions for brands
2023-07-15 07:23:59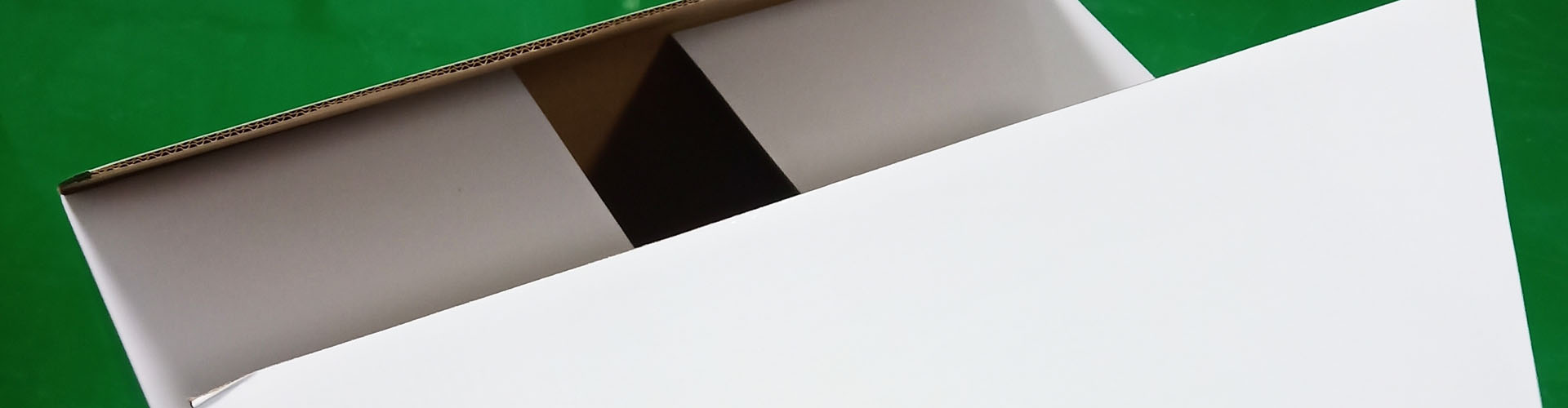
Reducing Waste and Increasing Recycling
2023-07-18 04:01:48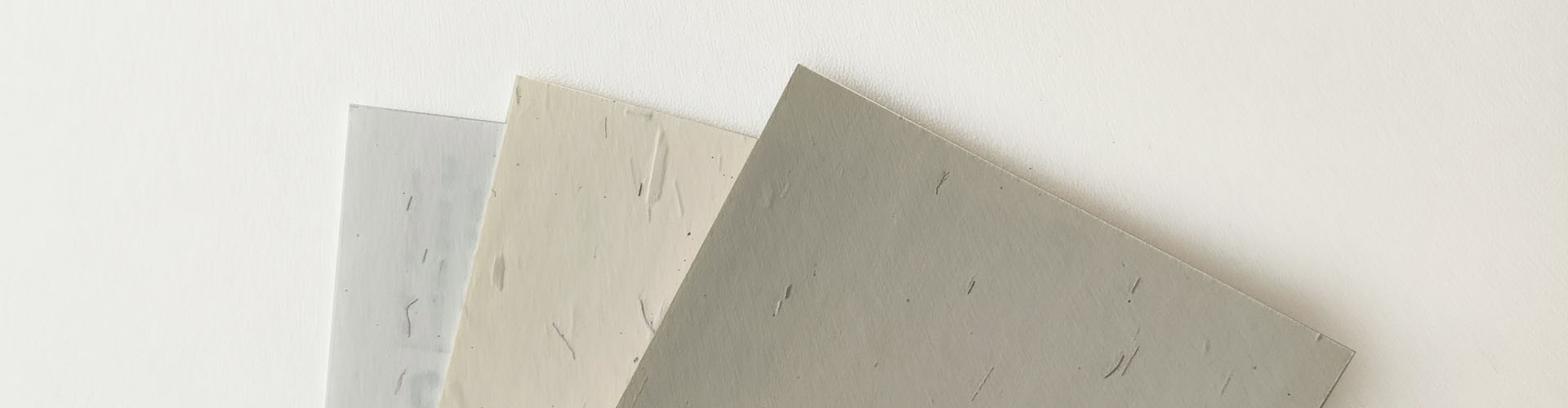
Promote sustainable practices throughout the supply chain
2023-07-18 06:35:56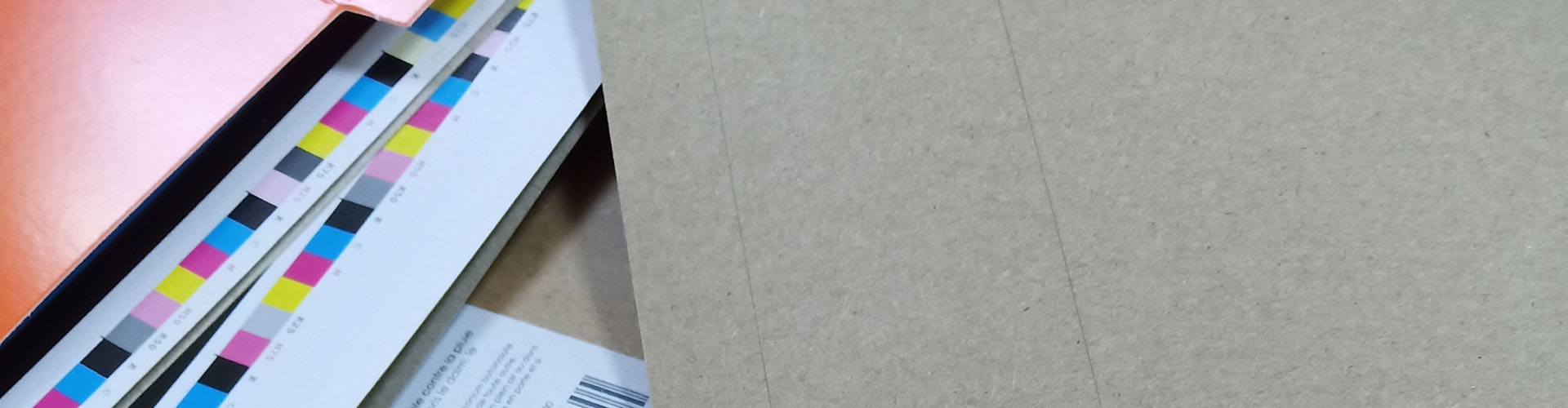
Focus on eco-friendly materials
2023-07-18 07:04:38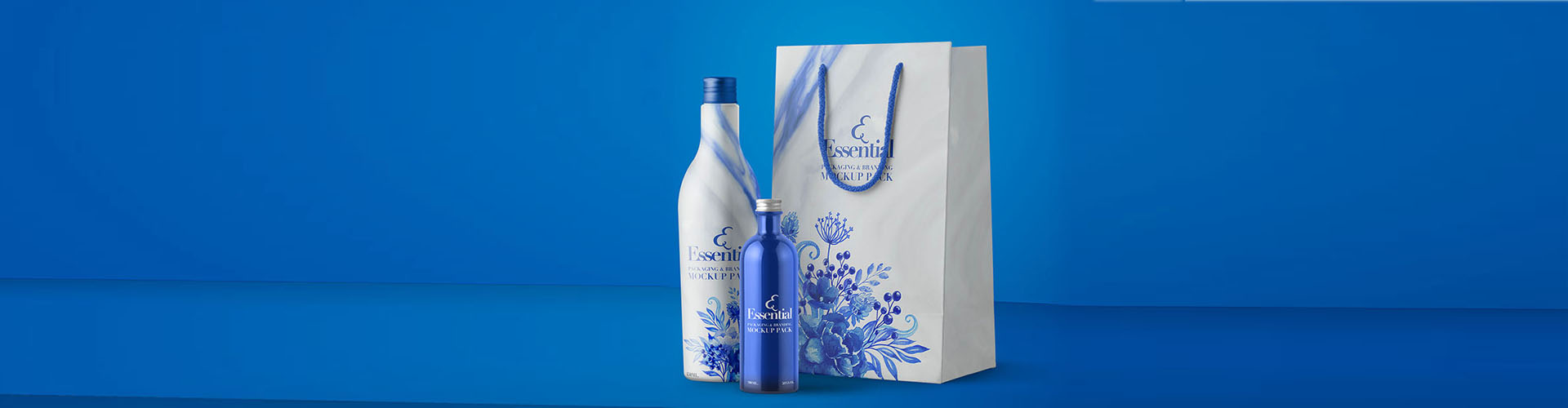
The packaging solution tailored for a specific product
2023-07-18 07:32:16POPULAR POSTS