Packaging boxes are an indispensable part of modern life, widely used in various industries such as food, pharmaceuticals, cosmetics, and electronics. In this article, we will delve into the production process of packaging boxes, from design to manufacturing, to help consumers better understand the process.
I. Design Stage
During the design stage of packaging boxes, designers need to consider the following aspects:
1. Product Characteristics: Designing packaging boxes requires consideration of product characteristics such as shape, size, and weight to ensure a perfect fit for the product.
2. Brand Image: Packaging boxes are an important part of a brand's image. Designers need to incorporate the brand image into the design to enhance its value.
3. Material Selection: Choosing the right materials for packaging boxes is crucial. Different materials have varying properties such as strength, water resistance, and moisture resistance. Designers need to select the most suitable materials based on product characteristics and brand image.
II. Plate Making Stage
During the plate making stage, designers need to transform the design into a printing plate using professional software such as Adobe Illustrator or CorelDRAW. Considerations during this process include:
1. Printing Method: There are various printing methods for packaging boxes, such as offset printing, letterpress printing, gravure printing and flexographic printing. Designers need to choose the most suitable method based on material and printing requirements.
2. Color Management: Color management is crucial during plate making. Designers need to select the most appropriate color management scheme based on printing requirements and material characteristics.
3. Layout Design: Layout design is an important part of plate making. Designers need to arrange the design according to printing requirements to ensure print quality.
III. Printing Stage
During the printing stage, printers need to consider several factors while adhering to plate making requirements:
1. Printing Equipment: Different printing equipment has varying characteristics such as speed and precision. Printers need to select the most suitable equipment based on printing requirements.
2. Printing Materials: The choice of printing materials is essential. Printers need to select the most suitable materials based on ink absorption and water resistance.
3. Printing Quality Control: Quality control during printing is crucial to ensure high-quality output.
IV. Cutting and Folding Stage
During the cutting and folding stage, printed sheets need to be cut and folded, considering the following factors:
1. Cutting Method: There are various cutting methods such as flat cutting, circular cutting, and die-cutting. Workers need to select the most suitable cutting method based on the shape and size of the packaging box.
2. Folding Method: Different folding methods include single fold, double fold, and triple fold. Workers need to choose the most suitable folding method based on the shape and size of the packaging box.
3. Quality Control: Quality control during cutting and folding is essential to ensure the quality of packaging boxes.
V. Gluing Stage
During the gluing stage, cut sheets need to be glued together, considering the following factors:
1. Gluing Method: Various gluing methods include hot melt gluing, cold melt gluing, and adhesive gluing. Workers need to choose the most suitable gluing method based on the material and shape of the packaging box.
2. Gluing Quality Control: Quality control during gluing is crucial to ensure high-quality bonding.
VI. Packaging Stage
During the packaging stage, packaging boxes need to be packed, considering the following factors:
1. Packaging Method: There are various packaging methods such as manual packaging and automatic packaging. Workers need to choose the most suitable packaging method based on the shape and size of the packaging box.
2. Packaging Quality Control: Quality control during packaging is essential to ensure high-quality packaging.
In conclusion, the production process of packaging boxes includes design, plate making, printing, cutting and folding, gluing, and packaging stages. Each stage requires consideration of different factors to ensure the quality and effectiveness of packaging boxes. As experts in the packaging industry, BEP Packaging will continue to focus on the production methods and technologies of packaging boxes to provide better services and support to industry users.
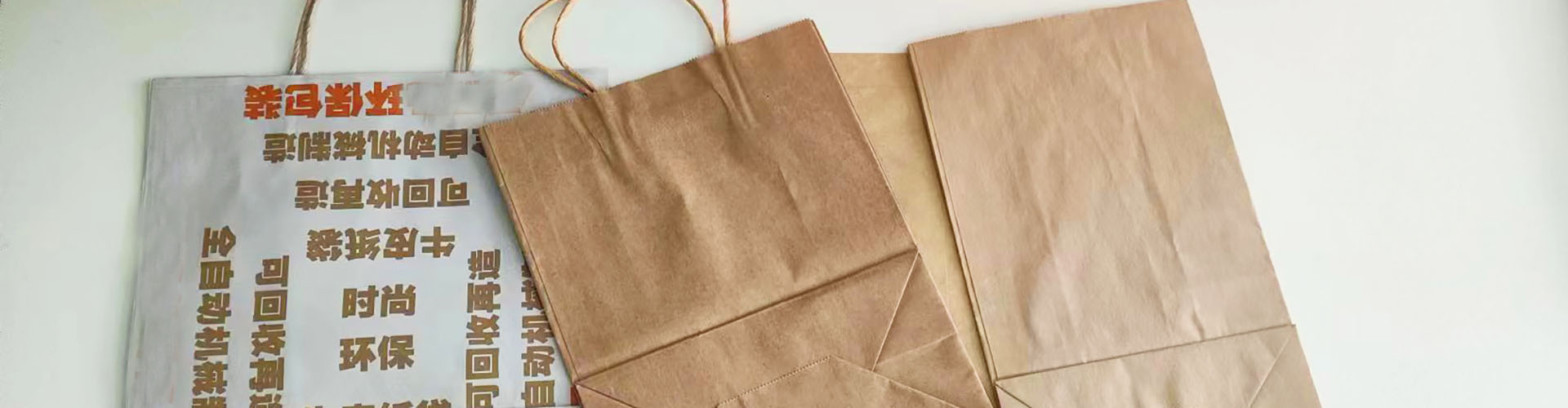
previous post
The Versatility and Environmental Benefits of Kraft Paper Packaging

next post
How can the printing of flexible packaging effectively avoid color difference
YOU MAY ALSO LIKE
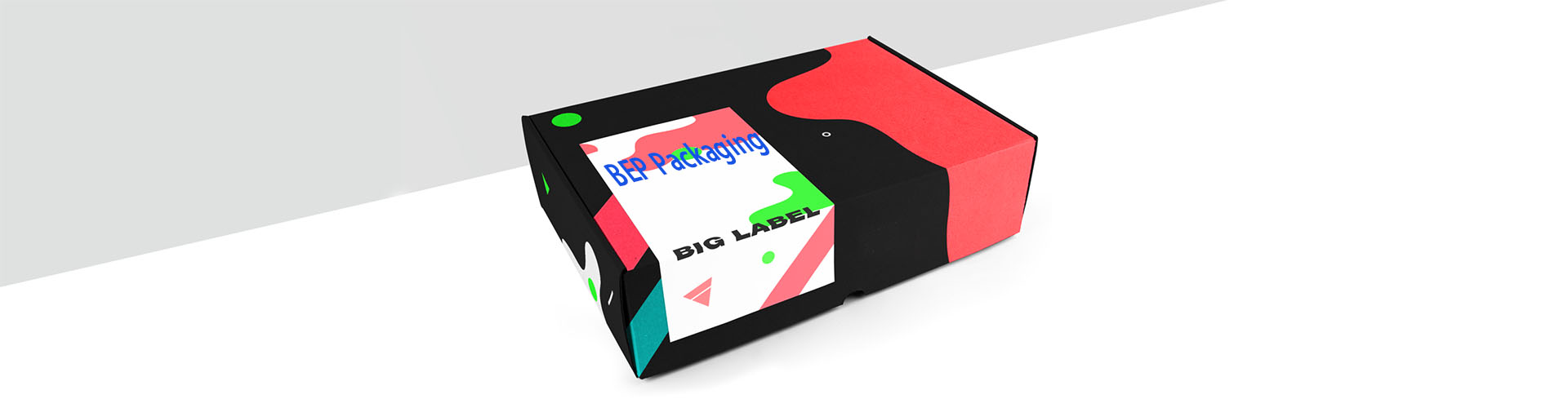
What is sustainable packaging
2023-05-05 02:03:21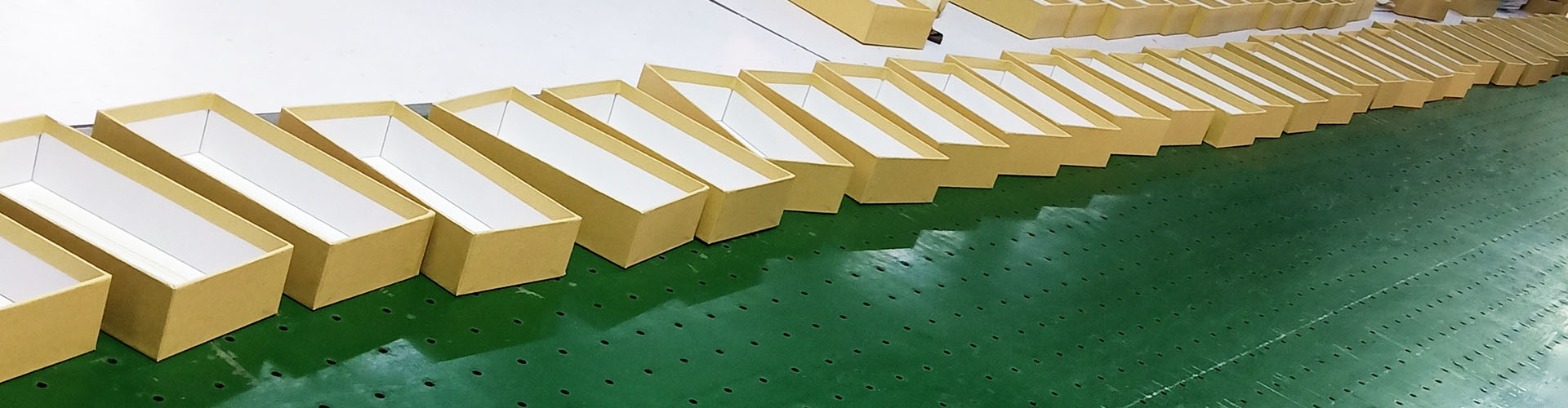
Integrated packaging solutions for brands
2023-07-15 07:23:59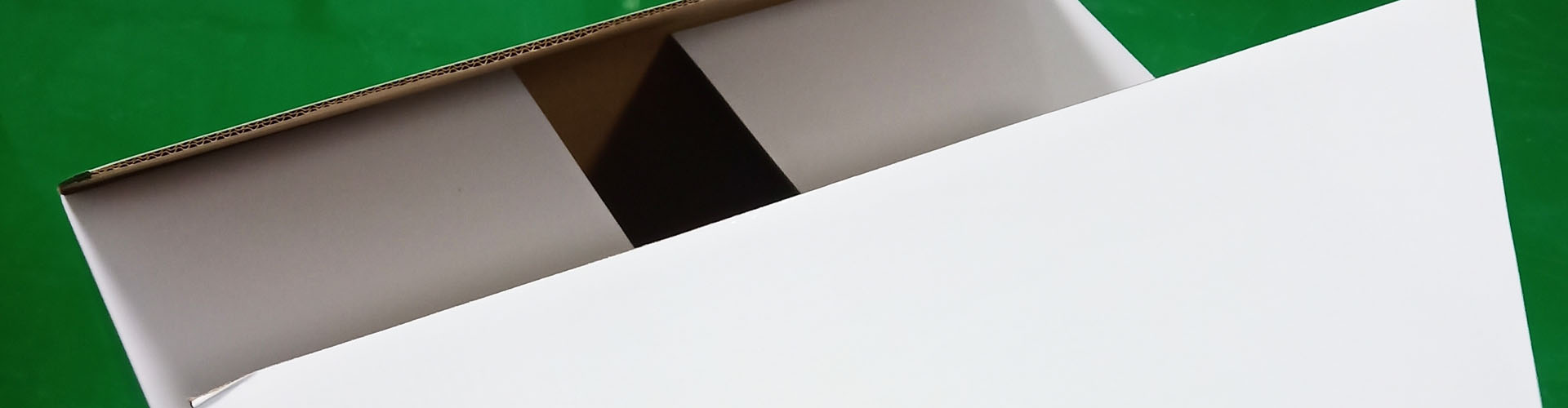
Reducing Waste and Increasing Recycling
2023-07-18 04:01:48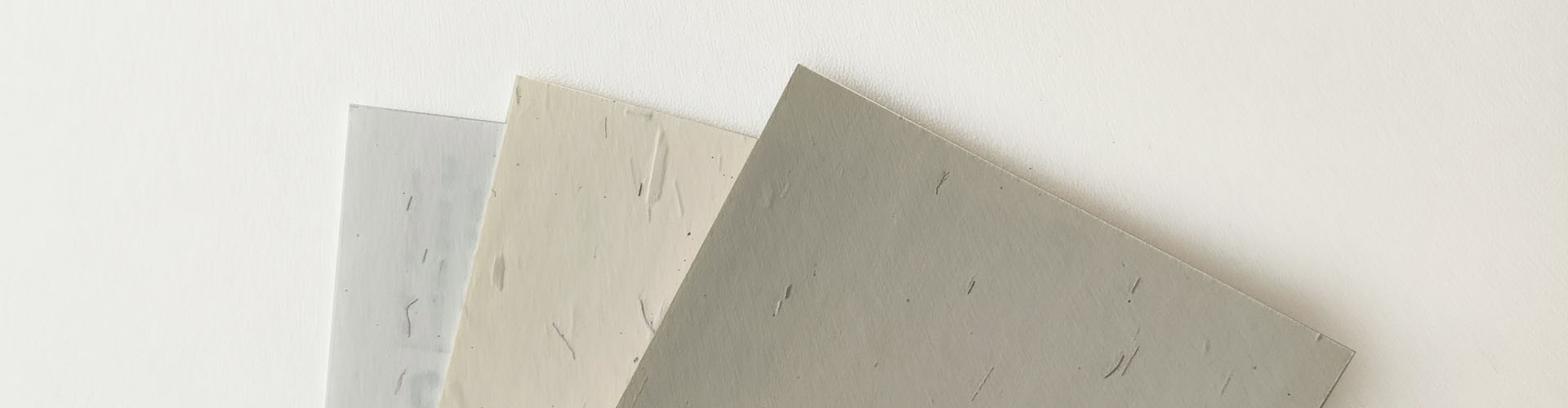
Promote sustainable practices throughout the supply chain
2023-07-18 06:35:56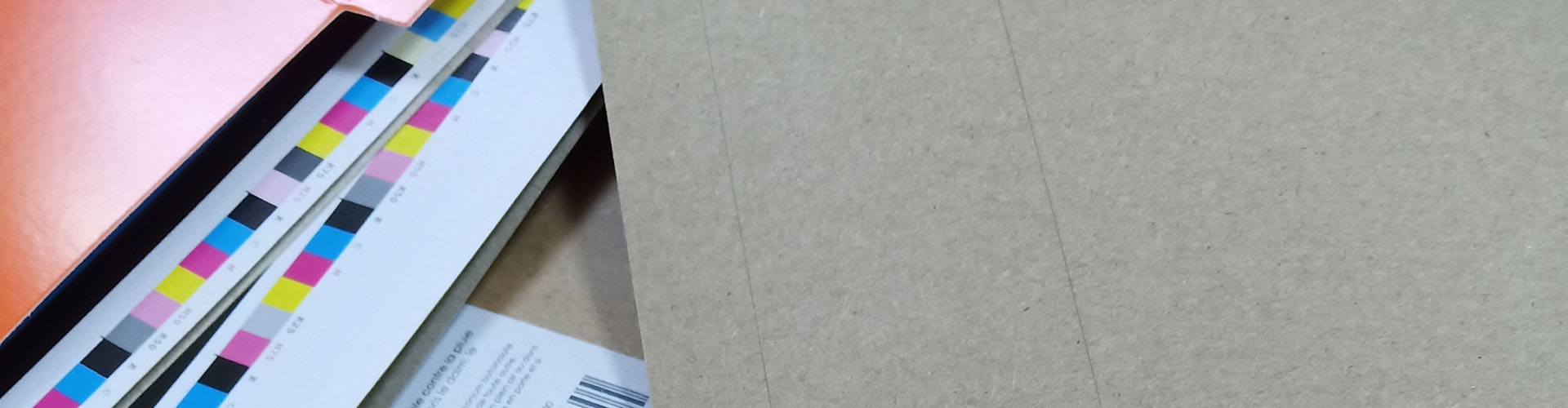
Focus on eco-friendly materials
2023-07-18 07:04:38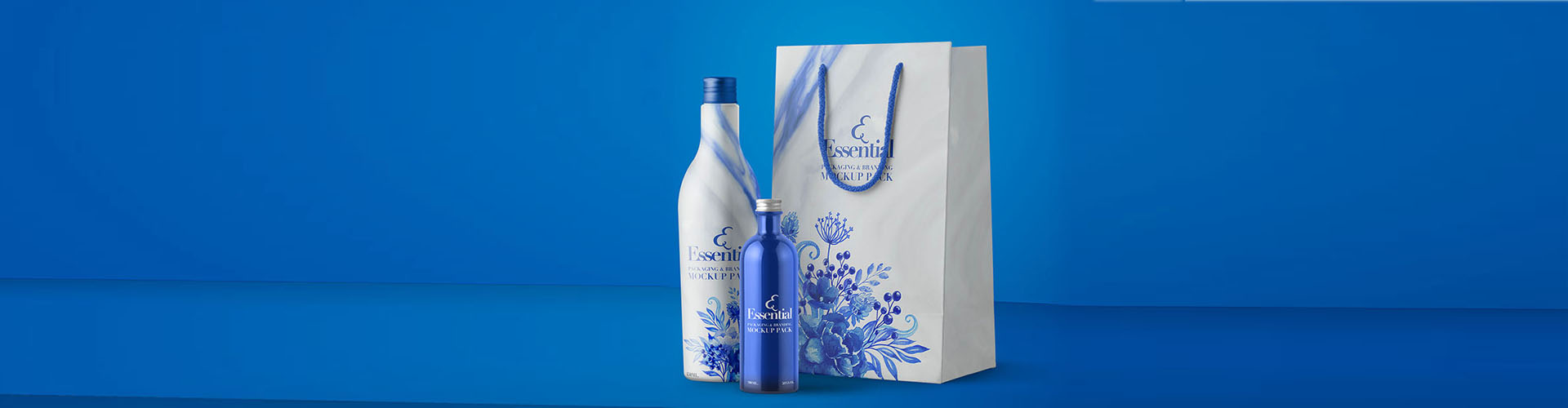
The packaging solution tailored for a specific product
2023-07-18 07:32:16POPULAR POSTS