In the printing process of flexible packaging, color deviation is a critical and focal point in the quality control process. Ensuring consistent color reproduction across a batch or multiple batches of printed materials is one of the most fundamental requirements and a challenge that needs to be addressed in the quality management of flexible packaging production. Many printing facilities struggle to effectively control color deviation due to the lack of a systematic color control method, leading to customer complaints, returns, and even claims.
Currently, many enterprises still rely on visual inspection to assess color deviation in printed materials, whether it meets the company's and the customer's color requirements. However, this approach introduces significant errors due to factors such as ink, lighting, environment, and observation methods, resulting in variations in the perceived colors. Larger enterprises have improved color judgment and identification by using color measurement instruments.
Regardless of whether visual inspection or color measurement instruments are used to assess color deviation, it is essential to identify the factors contributing to color deviation and implement effective color management to mitigate its occurrence.
I. Factors Contributing to Color Deviation
1. Ink Procurement
When selecting and purchasing ink, it is crucial to understand the ink system and the color deviation of each color. For example, primary red may have a blue hue, primary yellow may have a yellow or blue hue, etc. Therefore, ink selection should align with the product's printing color requirements. Additionally, archiving the original ink samples from the first use is essential for subsequent ink inspection and sampling. Ink usage typically involves small samples, trials, mid-scale trials, and large-scale trials before bulk usage. Archiving ink samples and printed samples for evaluation of ink color stability is the first step in controlling color deviation.
2. Sample Retention
Improper sample retention can lead to color deviation in printed materials. Many printing companies neglect standardized sample management, resulting in difficulties finding samples during printing or resorting to collecting samples from clients. Establishing a quality control department, setting up a color management center, and implementing proper sample retention practices are recommended for flexible packaging enterprises.
3. Sample Production
Samples are generally classified as customer-signed samples or customer-provided samples. It is crucial to securely store customer-signed samples for new layouts and ensure their inclusion in designated product archives. Communication with customers regarding color aspects before plate making is essential to understand acceptable color deviation and requirements. Plate making should align with the customer's color requirements to effectively reduce color deviation issues during color matching.
4. Sample Storage
After confirming the printing of new or revised products, timely sample retention is necessary. The quality control department should verify and standardize retained samples, ensuring clarity, accurate registration, and compliance with signed and matched color requirements. When composite films are produced, samples should be retained as per notification requirements, with emphasis on print clarity, absence of quality issues, accurate registration, and compliance with signed and matched color requirements.
5. Printing
Post-printing maintenance and cleaning of plate rollers are critical to prevent dot clogging and ensure color stability. Monitoring the wear rate of plate rollers can assist in predicting maintenance needs. Additionally, precise color matching during ink adjustment using consistent ink sources and accurate measurements is essential for effective color control.
6. Color Adjustment
The core of color deviation control lies in the printing color adjustment process. It is crucial for operators to have a comprehensive understanding of ink colors and employ standardized methods for ink adjustment. Accurate weighing and recording of ink addition are necessary when using residual ink for adjustment. Specialized ink adjustment for spot colors should involve precise measurement and comparison against standard samples. Once the color match exceeds 90% of the standard sample, viscosity adjustment can be performed.
7. Ink Scraper Blades
Frequent movement of ink scraper blades during production can disrupt ink transfer and color reproduction. Proper positioning and angle adjustment of ink scraper blades are essential to ensure uniform ink layering across the print surface.
8. Viscosity Control
Pre-production viscosity adjustments should align with estimated machine speeds, followed by a 10-minute wait after solvent addition before starting production. Measuring viscosity at regular intervals during production can establish standard viscosity values for consistent control and reduction of color deviation issues due to viscosity changes.
9. Production Environment
Maintaining relative humidity between 55% and 65% in the production environment is ideal for optimal ink transfer and print quality. Controlling relative humidity effectively improves ink transfer performance and helps mitigate color deviation issues.
10. Raw Materials
The surface tension of raw materials determines ink wetting and transfer effects on substrates, influencing color reproduction on film surfaces and contributing to color deviation.
11. Quality Awareness Enhancement
Enhancing quality awareness among production and quality control personnel is crucial for meticulous attention to detail. Strict adherence to standards during sample matching, first-article inspection, quality control implementation, ink replacement, and cleanliness maintenance ensures uniformity in product coloration and minimizes color deviation issues.
In conclusion, while color deviation is inevitable in the printing of flexible packaging, it is essential to focus on mitigating or reducing its occurrence through improved practices. Analyzing the various factors outlined above provides valuable insights into identifying methods for improvement and effective color deviation control. The principle of prevention as a primary approach, complemented by improvement, is crucial for standardizing sample management and avoiding color deviation, ensuring minimal noticeable color variation across batches of products.
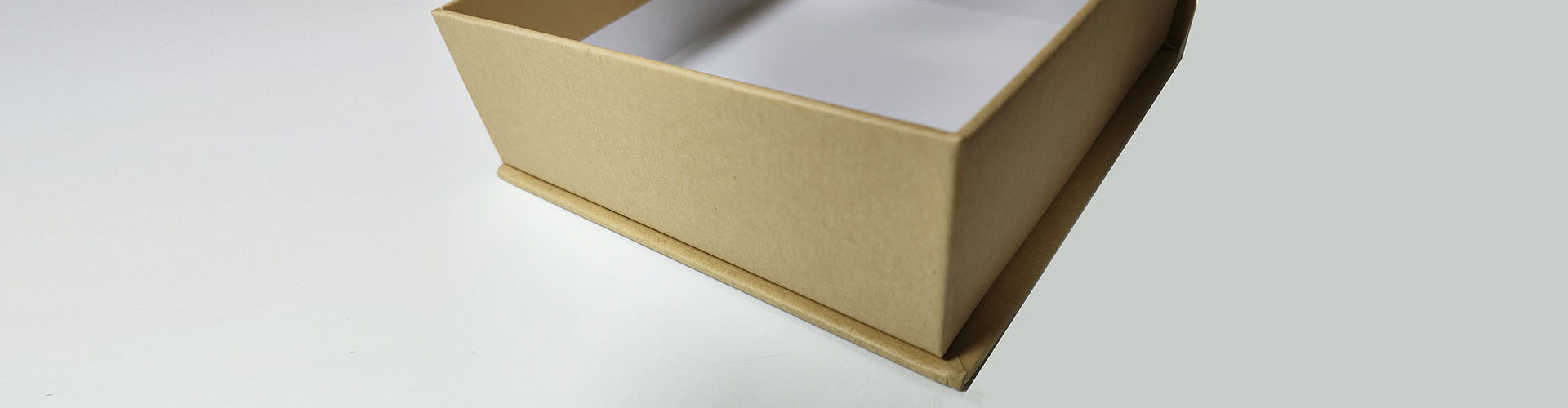
previous post
How to make a packaging box
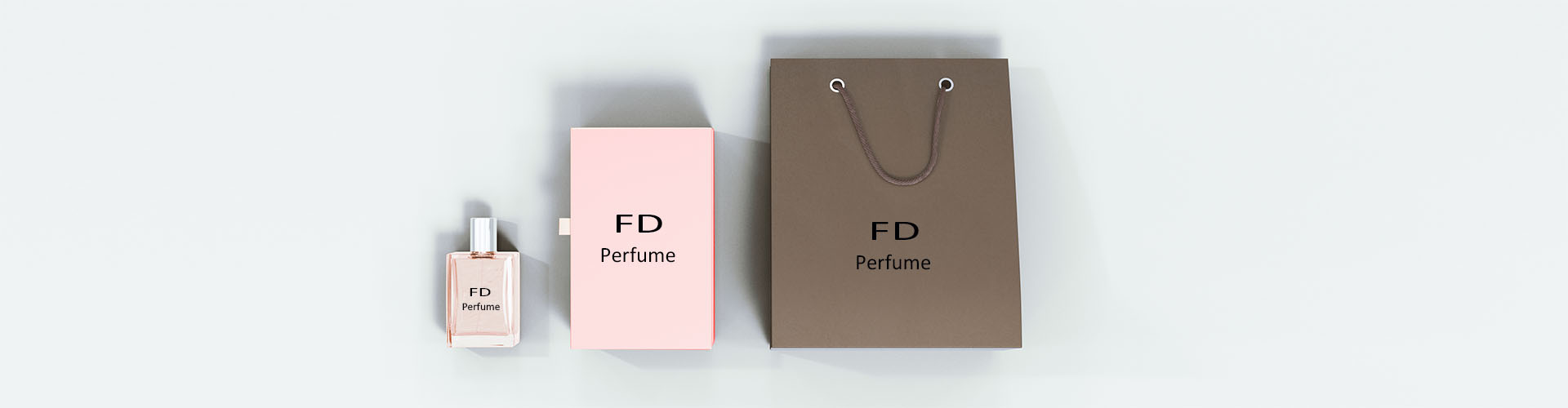
next post
The Evolution and Development of Cosmetics Packaging
YOU MAY ALSO LIKE
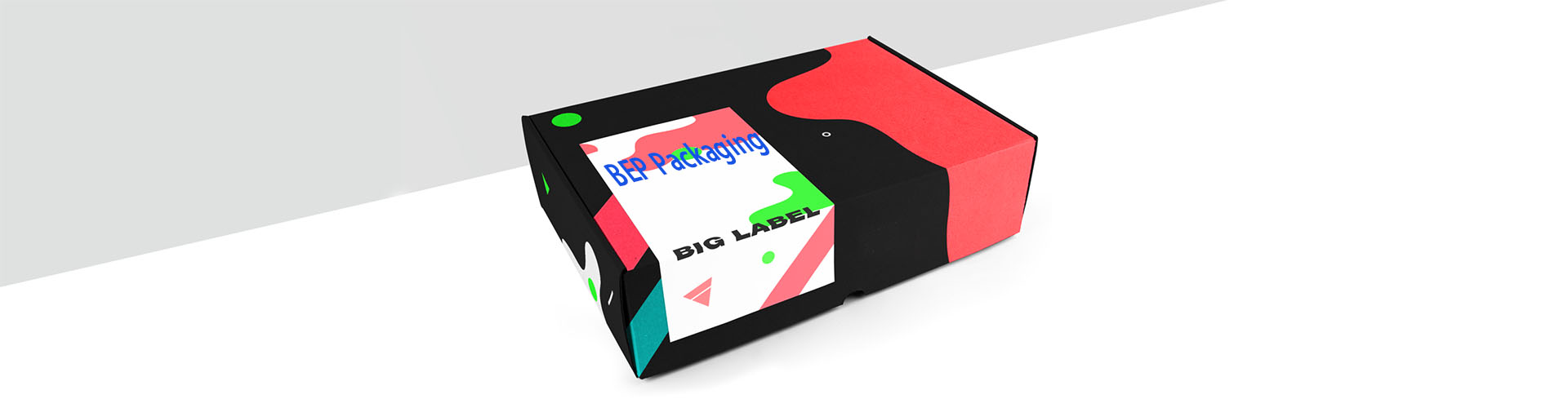
What is sustainable packaging
2023-05-05 02:03:21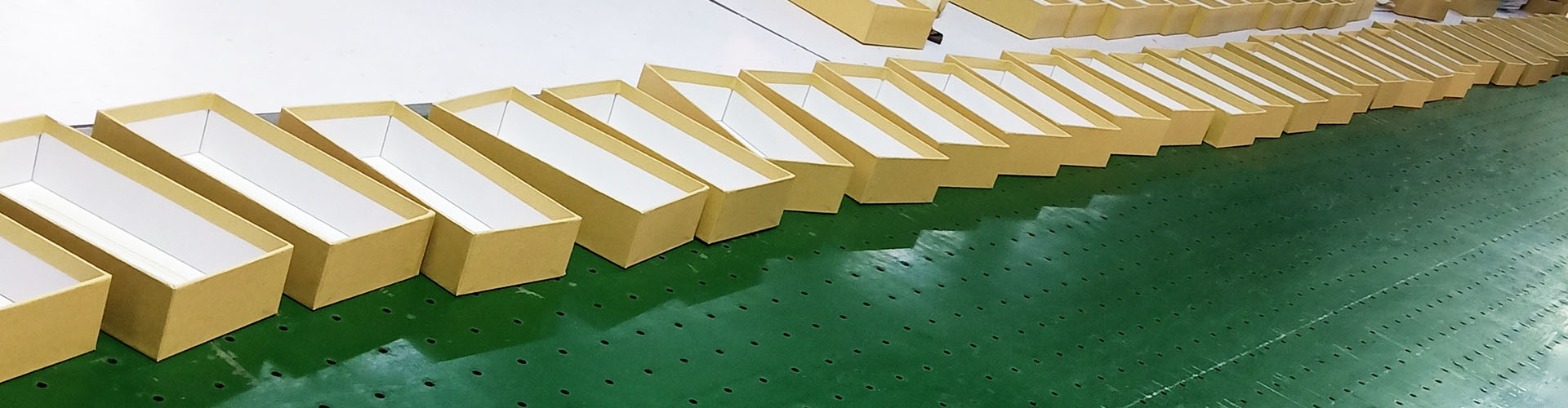
Integrated packaging solutions for brands
2023-07-15 07:23:59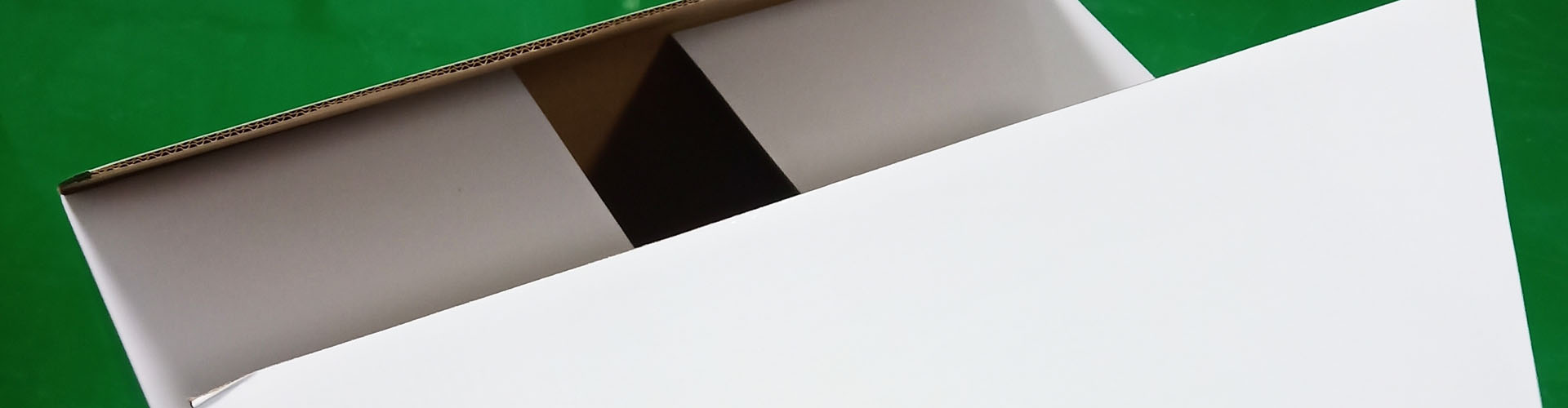
Reducing Waste and Increasing Recycling
2023-07-18 04:01:48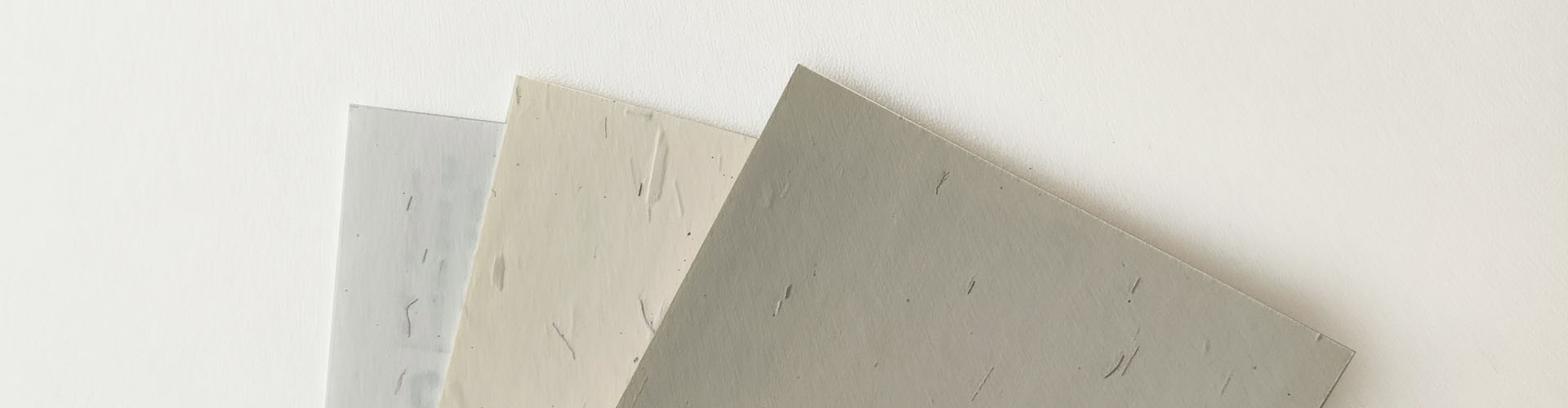
Promote sustainable practices throughout the supply chain
2023-07-18 06:35:56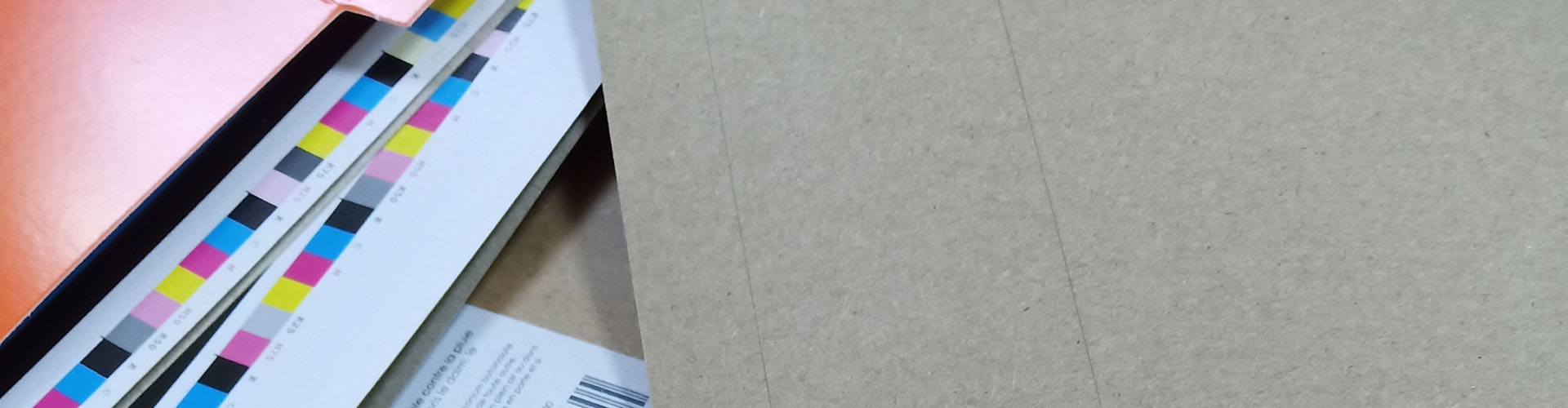
Focus on eco-friendly materials
2023-07-18 07:04:38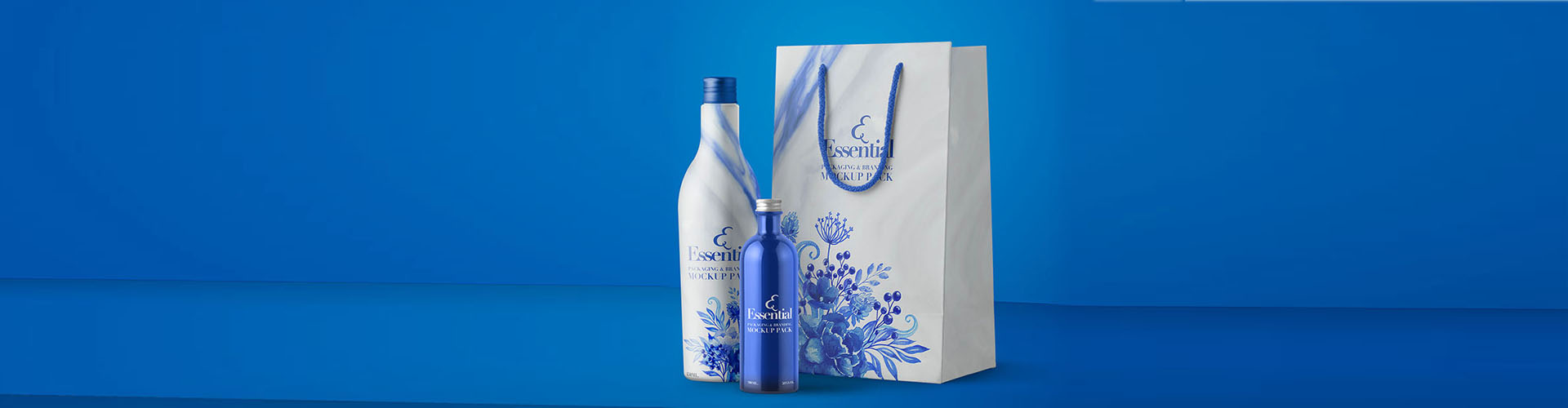
The packaging solution tailored for a specific product
2023-07-18 07:32:16POPULAR POSTS