The printing of packaging products is an important means and approach to increase the added value of products, enhance product competitiveness, and explore new markets. The packaging company should understand the necessary knowledge of packaging printing processes to make the designed packaging more functional and aesthetically pleasing. Different packaging materials require different printing processes, so I will share the relevant knowledge of printing processes with you.
Packaging printing plays a crucial role in enhancing the value and competitiveness of products, as well as expanding market opportunities. It is important to have a good understanding of the various printing techniques and their applications in order to create packaging that is both functional and visually appealing.
The choice of printing process is largely dependent on the type of packaging material being used. Different materials may require different printing methods to achieve the desired results. By understanding the capabilities and limitations of each printing technique, designers can make informed decisions to optimize the appearance and performance of the final packaging product.
Paper packaging and printing technology
1. Printing Methods
Paper packaging can be printed using a variety of techniques, each with its own unique characteristics and advantages. The main printing methods used for paper packaging include:
(1) Relief Printing (Letterpress Printing)
In relief printing, the image areas on the printing plate are raised above the non-image areas. When the inked roller passes over the plate, the ink is only transferred to the raised image areas, while the recessed non-image areas remain ink-free. This creates a raised, three-dimensional effect on the printed surface, where the image areas stand out slightly compared to the surrounding paper. The edges of the printed lines and dots in relief printing are typically clean and well-defined.
(2) Gravure Printing
Intaglio printing is the opposite of relief printing. In this method, the image areas on the printing plate are recessed below the surface, forming grooves or depressions. The ink is applied to these recessed areas, while the raised, non-image areas of the plate remain ink-free. When the paper is pressed onto the inked plate, the ink is transferred from the recessed areas to the paper, resulting in a printed image with a thick, pronounced ink layer. Intaglio printing is known for its rich, vibrant colors, high print durability, and consistent print quality, as well as its relatively fast printing speed, making it a popular choice for various packaging applications.
(3) Offset Printing
Offset printing is based on the principle of the repulsion between oil and water. The printing plate has image areas that are lipophilic (oil-loving) and non-image areas that are hydrophilic (water-loving). When the ink is applied, the image areas repel the water and attract the ink, while the non-image areas, having absorbed water, resist the ink. The ink is then transferred from the plate to a rubber-covered cylinder (the "offset" cylinder) and then to the paper or substrate. Offset printing is a widely used method due to its simplicity, cost-effectiveness, and versatility in terms of the range of materials and designs it can accommodate.
(4) Screen Printing
Screen printing, also known as silk-screen printing, involves forcing ink through a fine mesh screen that has been selectively blocked or stenciled to create the desired image. The ink is pushed through the open areas of the screen using a squeegee, while the blocked areas prevent the ink from transferring to the substrate. This method allows for the printing of large, solid areas of color and is particularly well-suited for packaging applications that require high-opacity, vibrant, or specialized ink formulations, such as metallic, pearlescent, or UV-curable inks.
Each of these printing methods has its own unique characteristics, advantages, and applications, allowing packaging designers and manufacturers to select the most appropriate technique to achieve the desired visual and functional effects for their packaging products.
2. Surface Finishing Techniques
In addition to the various printing methods, there are also several surface finishing techniques commonly used in paper-based packaging printing:
(1) Hot Stamping (Foil Stamping)
Hot stamping involves creating a raised, metallic image or text on the printed surface. A heated, die-cut metal stamp is pressed onto a layer of metallic foil, causing the foil to transfer and adhere to the substrate. This process can create striking effects, such as gold, silver, holographic, or colored metallic accents on the packaging.
Tip: There is a wide variety of foil materials available, including gold, silver, holographic, black, red, green, and more.
(2) Lamination
Lamination is a post-printing surface treatment process where a transparent plastic film is applied over the printed surface using a laminating machine. This provides a smooth, glossy, and durable finish to the printed piece, improving resistance to dirt, water, and abrasion.
Tip: Laminated printed products have a smoother, more polished appearance and enhanced protection against external factors.
(3) Embossing
Embossing is a technique that uses the high pressure of a letterpress printing machine to create raised or recessed designs on the printed substrate. This allows for the creation of three-dimensional, tactile effects on the packaging, adding depth and visual interest to the design.
Note: Embossing is often used as a post-printing process on printed materials and paper containers. In addition to packaging, it is also applied to labels, stickers, books, calendars, and greeting cards.
These surface finishing techniques can be used in combination with the various printing methods to enhance the visual appeal, functionality, and overall quality of the final packaging product.
(4) UV Anti-Metal Etching Printing
UV anti-metal etching printing, also known as matte or sand-effect printing, is a technique applied to substrates with a metallic mirror-like finish (such as gold or silver cardboard). A layer of uneven, semi-transparent ink is printed and then cured using ultraviolet (UV) light, creating an effect that resembles a metal surface that has been etched or sandblasted.
Note: UV anti-metal etching inks can produce a velvety matte or satin-like finish, making the printed product appear soft, dignified, elegant, and luxurious.
In addition to the printing processes mentioned above, paper packaging printing also includes the following techniques:
1. Holographic Effects: Printing that creates iridescent, rainbow-like visual effects.
2. Die Cutting and Creasing: Shaping the substrate through the use of cutting and scoring dies.
3. Thermal Transfer: Printing using heat-activated inks or foils.
4. Raised Ink (Plastic Coating): Applying thick, relief-like ink or plastic coatings.
5. Frosting/Ice Effects: Creating a frosty, icy appearance on the printed surface.
6. Scratch-off Coatings: Printing with a removable, opaque coating that reveals hidden information or designs.
These additional printing and surface finishing techniques further expand the range of visual and tactile effects that can be achieved on paper-based packaging, allowing designers to create unique and captivating packaging solutions.
Common Printing Techniques in Packaging
Four-Color Printing
1. The four-color printing process refers to the use of four specific ink colors: Cyan (C), Magenta (M), Yellow (Y), and Black (K). By combining these four ink colors, it is possible to reproduce a wide range of colors and create full-color images and text.
2. Four-color printing is the most common and widely used printing technique. The final printed result can vary depending on the substrate material.
Spot Color Printing
1. Spot color printing involves the use of a single, special-mixed ink color, which can produce more vibrant and saturated colors compared to the colors achieved through four-color mixing.
Commonly used spot colors include metallic gold and silver.
2. There are many available spot color options, as referenced in Pantone color guides. Spot colors are not suitable for gradients, so four-color printing may be necessary to achieve such effects.
1. After printing, a transparent plastic film is laminated onto the printed surface through a heat-based process. This serves to protect the printed piece and add a glossy sheen.
2. Varnish coating is a fundamental surface treatment for paperboard packaging. A similar process, known as gloss coating, can also be used to enhance the surface smoothness and durability of the printed material.
1. After printing, a transparent plastic film is laminated onto the printed surface through a heat-based process. This provides protection and a matte, non-glossy finish to the printed piece.
2. Matte lamination is a fundamental surface treatment for paperboard packaging. Similar to gloss coating, but matte lamination can enhance the stiffness and tear resistance of the paper material.
Specific areas of the printed piece are selectively coated with a UV-curable varnish to add a glossy, raised effect, enhancing the three-dimensional appearance of the design.
1. Foil stamping is a process that uses heat and pressure to transfer metallic foil from a carrier material onto the printed substrate, creating a special metallic, glossy effect.
2. The foil materials come in a variety of colors, such as gold, silver, red, green, and blue. However, foil stamping is a single-color process, and not all color options may be readily available in the market.
3. When combined with a matte coating process, the foil stamping effect will not be visible, as the matte finish covers the metallic appearance.
1. Embossing involves the use of a set of corresponding male and female dies, which are pressed against the substrate material to create a raised, relief-like pattern or text.
2. This technique can be applied to a variety of paper thicknesses, but is not suitable for use on paperboard.
1. The process of using a printing machine to spray identify markings (such as production dates, expiry dates, batch numbers, company logos, etc.) directly onto products.
2. Ink jet printing allows for the flexible application of simple text and graphics.
Thermoforming (Vacuum Forming)
1. Thermoforming uses transparent materials, primarily PVC, PE, or PET, to create packaging solutions.
2. The thermoformed material can directly replace paperboard in constructing boxes, or be used in conjunction with card manufacturing.
3. Thermoformed trays can be used to securely hold and protect products inside the packaging.
4. The thermoformed parts can be screen printed, offset printed, or foil stamped.
5. Printing on thermoformed parts is possible, but the cost is generally higher, so screen printing is typically used for smaller production runs.
EVA (Ethylene-Vinyl Acetate)
1. EVA is a copolymer of ethylene and vinyl acetate, with properties such as good flexibility, shock absorption, anti-slip, and high compressive strength.
2. EVA is used in packaging interiors to secure and protect products.
3. It is available in a variety of colors and can be flocked or wrapped in fabric to enhance the visual appeal.
1. Foam is a porous, lightweight material with good elasticity. The density of the foam determines its level of flexibility.
2. Foam is used in packaging interiors to secure and protect products.
3. Foam comes in different colors and is generally used as-is, without additional finishing processes.
Common Packaging Materials
Solid Bleached Sulfate (SBS) Board
1. SBS is a common paperboard material, available in a wide range of thicknesses from 80 gsm to 400 gsm. For thicker boards, lamination of two sheets may be required.
2. The material has a glossy side and a matte side, with only the glossy side being suitable for printing.
3. SBS board allows for printing in a variety of colors, without any limitations.
4. Common surface finishing techniques for SBS board include varnishing, UV coating, foil stamping, and embossing.
Corrugated Cardboard
1. Corrugated board is more rigid and has higher load-bearing capacity compared to regular paper.
2. Common types include single-wall, double-wall, and triple-wall corrugated board.
3. Corrugated board can be printed in various colors, but the print quality is generally not as high as SBS.
4. The common surface finishing techniques for corrugated board are varnishing, UV coating, foil stamping, and embossing.
1. Paperboard is used for constructing gift box structures, with a layer of SBS or specialized paper laminated on the surface.
2. Common paperboard colors include black, white, gray, and yellow.
3. Paperboard is available in different thickness grades, selected based on the required load-bearing capacity.
4. If the surface is laminated with SBS, the finishing techniques are the same as for SBS packaging. If a specialized paper is used, the options are generally limited to foil stamping, with limited printing capabilities and lower print quality.
These are some of the most commonly used paperboard-based packaging materials, each with their own unique characteristics, strengths, and suitable surface finishing techniques.
1. There are many types of specialty papers used in packaging, including embossed papers, patterned papers, pearl effect papers, metallic patterned papers, and gold papers.
2. These specialty papers undergo specialized treatments to enhance the tactile and visual qualities of the packaging. Papers with embossed or patterned textures cannot be printed, and can only be foil stamped, while metallic and iridescent papers can be printed in full color.
Holographic/Metallic Papers
1. These papers utilize UV transfer printing technology, where a UV-curable ink is first coated onto the paper surface using a rubber roller, and then a holographic or specific pattern film is transferred onto the printed paper to create a holographic or metallic effect.
2. Holographic/metallic papers can only be printed using a UV printing press, but this allows for a wide range of visual effects and different levels of glossiness. However, these papers are generally more expensive compared to regular papers.
BEP Packaging is a leading provider of diverse packaging solutions, catering to the needs of a wide range of industries. The company offers a comprehensive range of packaging materials. The company's expertise extends to rigid paper packaging, rigid paperboard box, and rigid paper containers, catering to the needs of diverse industries.
In addition to its extensive product portfolio, BEP Packaging offers comprehensive packaging services, including the selection of optimal packaging materials, design, and production. As a reputable packaging company, BEP Packaging serves clients nationwide, providing customized solutions and personalized business packaging to meet their unique requirements.
Whether you're in need of rigid cardboard boxes, rigid paper boxes, rigid paper cans, or plastic folding cartons, the team of packaging experts is dedicated to delivering high-quality, innovative, and efficient packaging solutions tailored to your specific needs.
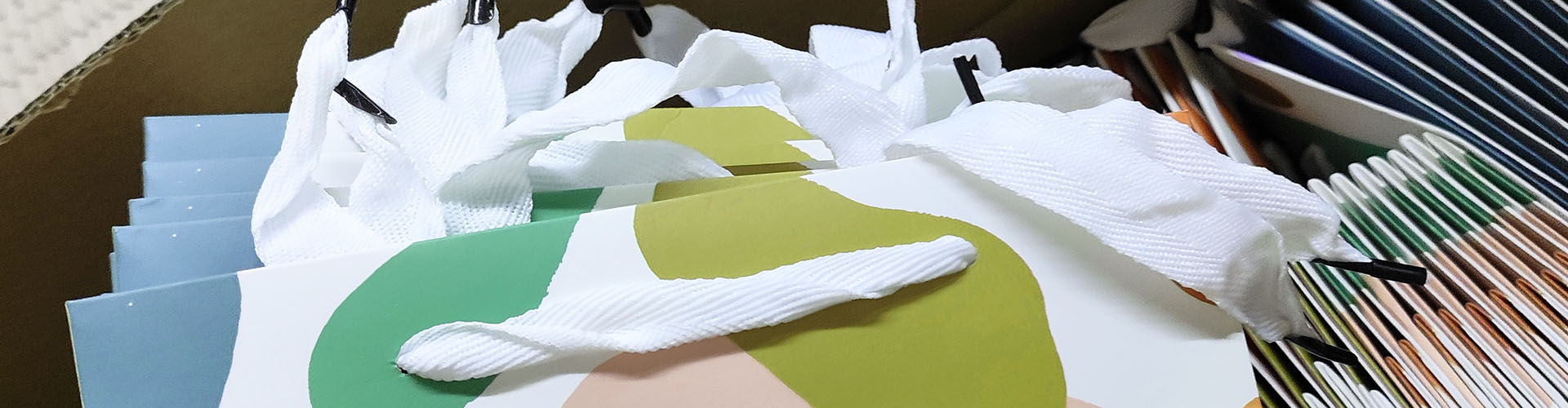
previous post
Comparison of Common Bag Materials for Retail Packaging
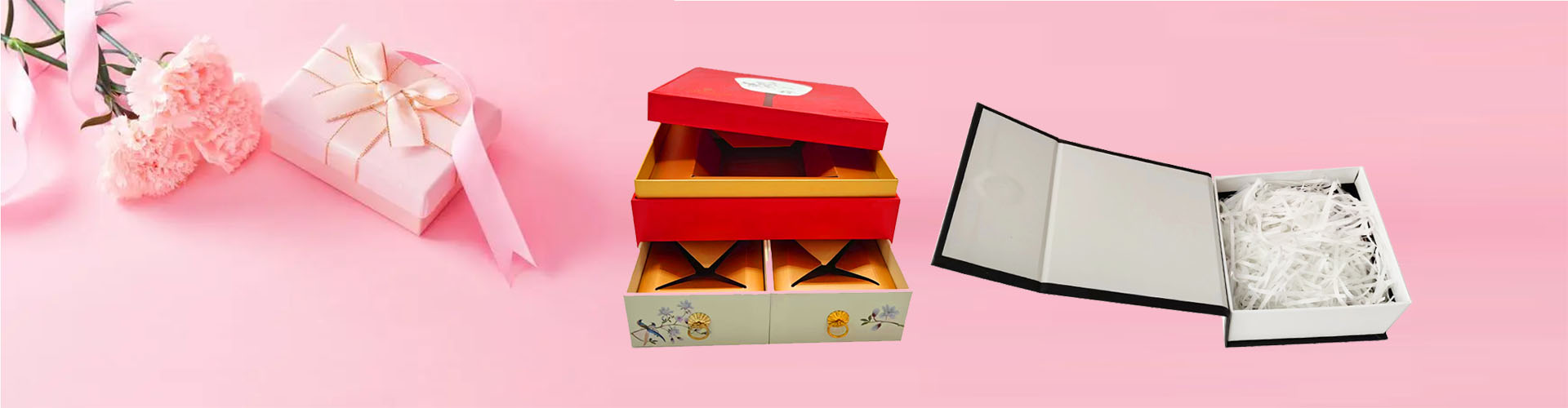
next post
Luxurious Flip Top Magnetic Gift Box for Her
YOU MAY ALSO LIKE
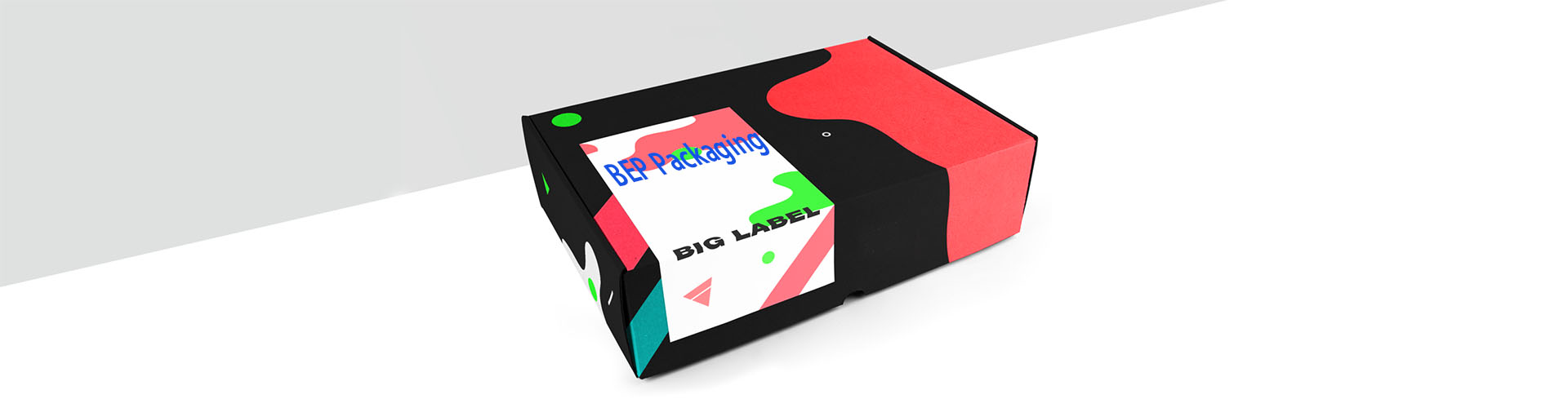
What is sustainable packaging
2023-05-05 02:03:21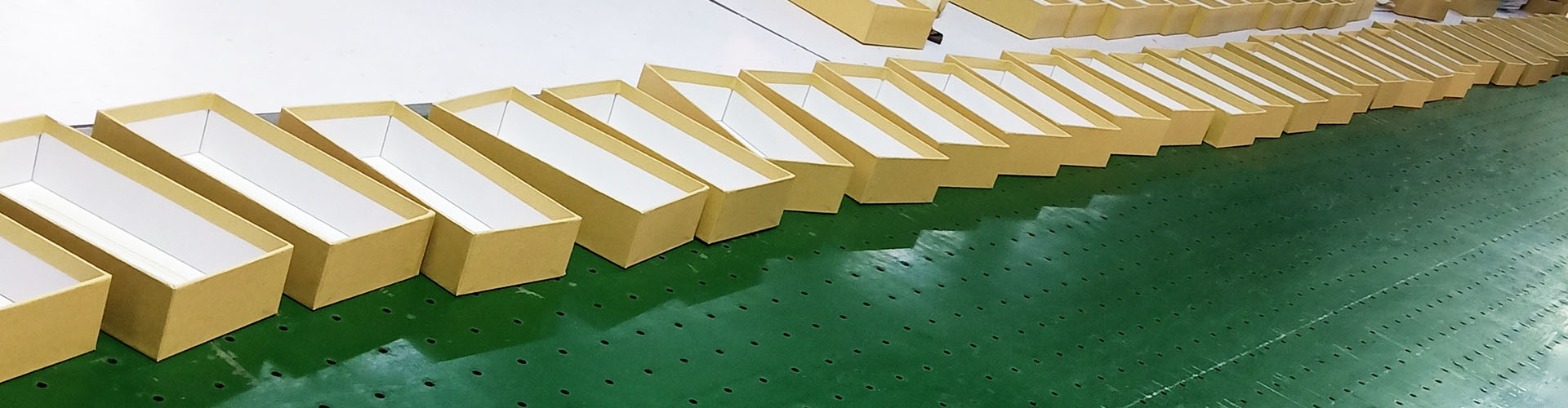
Integrated packaging solutions for brands
2023-07-15 07:23:59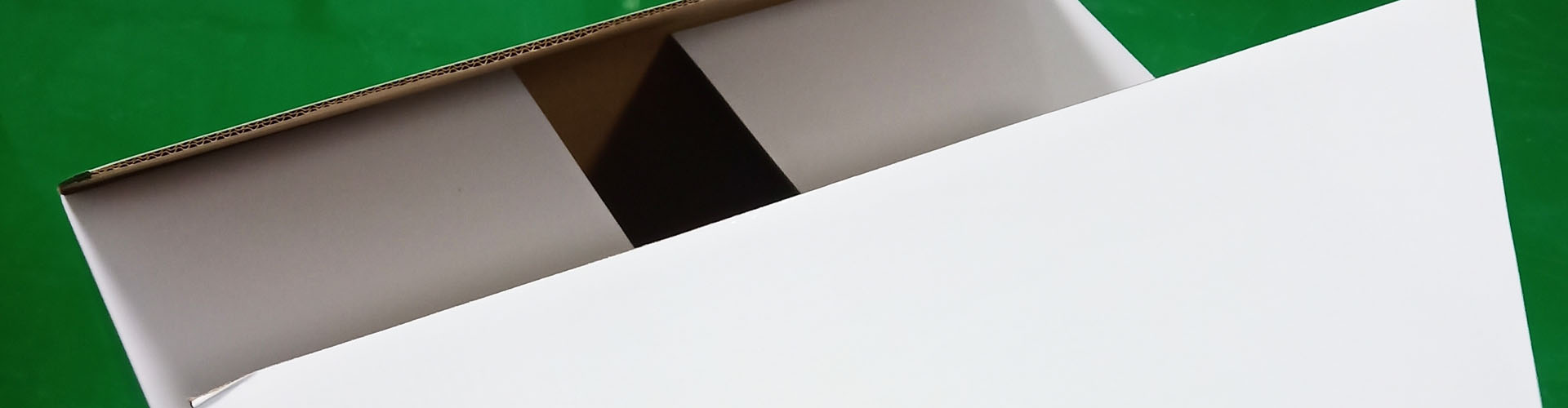
Reducing Waste and Increasing Recycling
2023-07-18 04:01:48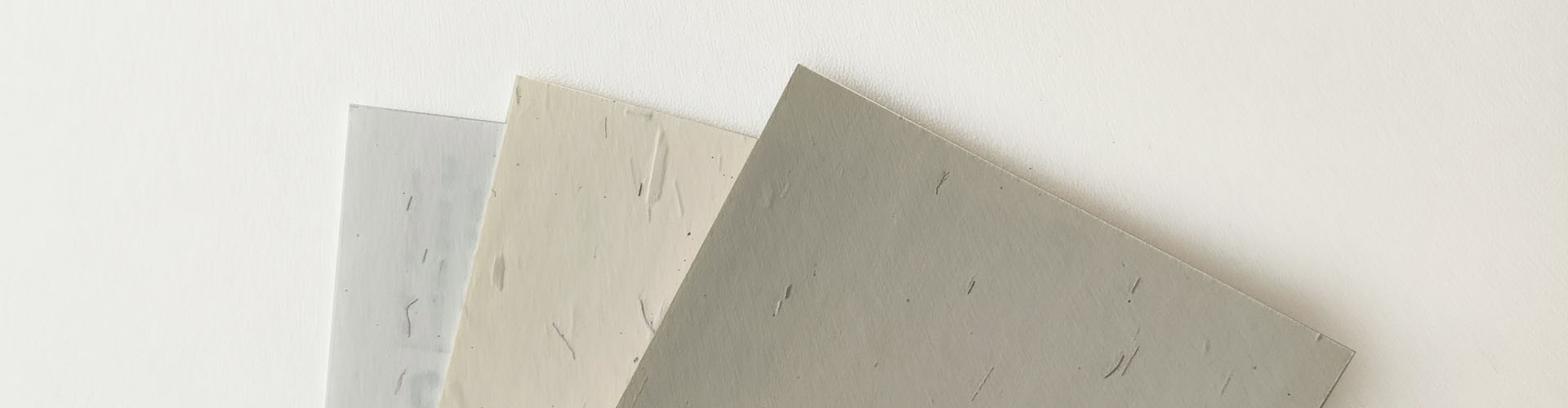
Promote sustainable practices throughout the supply chain
2023-07-18 06:35:56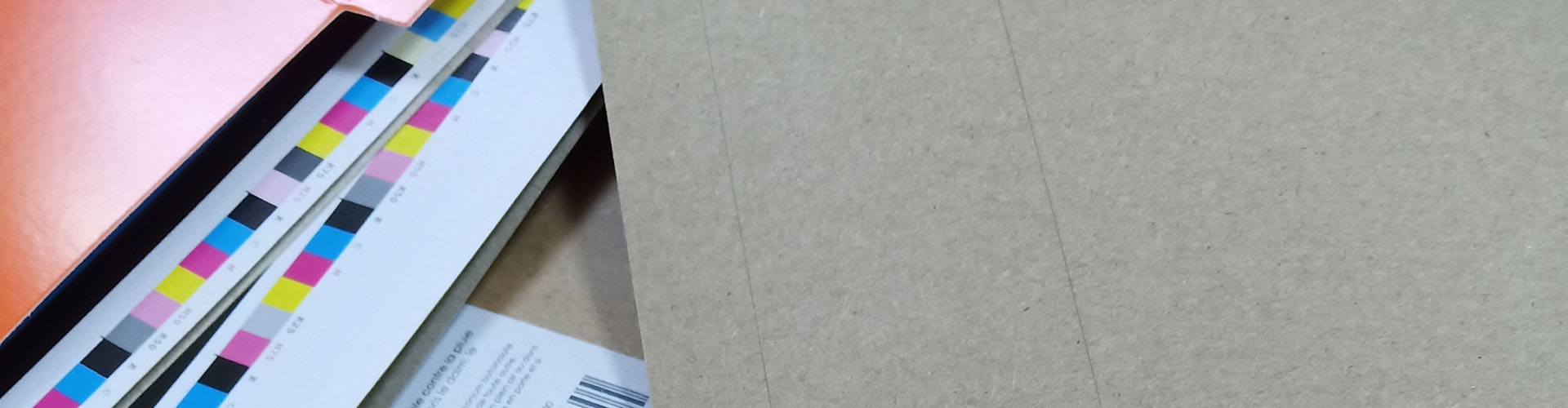
Focus on eco-friendly materials
2023-07-18 07:04:38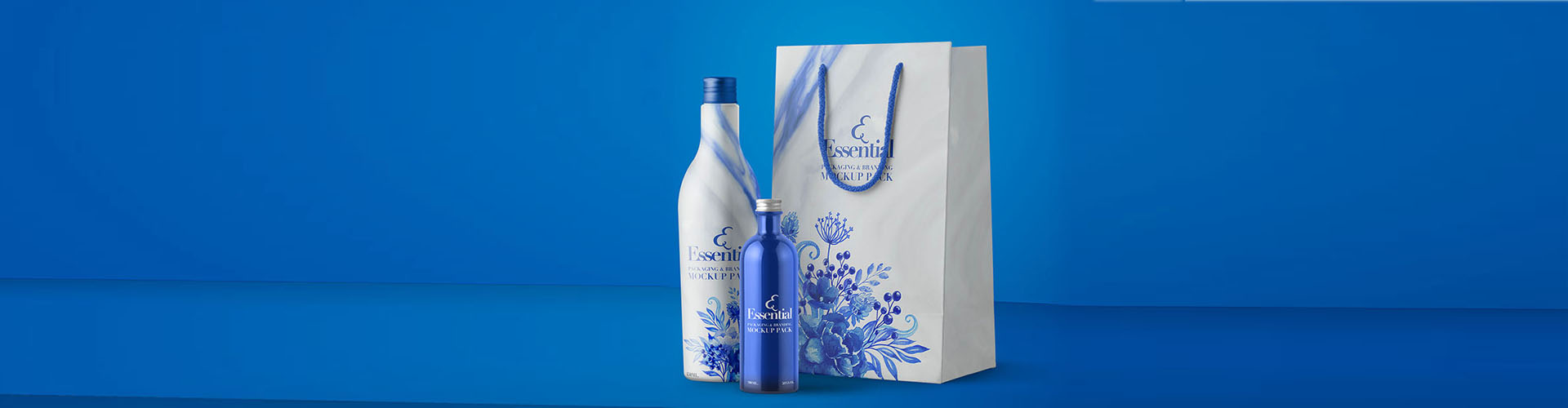
The packaging solution tailored for a specific product
2023-07-18 07:32:16POPULAR POSTS